Design layout of the joining zone – Part 2
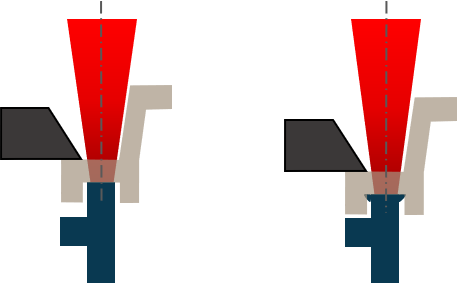
The following criteria are specifically relevant for the individual process variants and must be taken into account accordingly when it comes to the design layout of the joining zone.
CONTOUR WELDING-TOLERANCES – As no relative movement of the joining partners to each other can take place in a contour welding process, but thermal contact between the two is equally necessary, the requirements for the tolerances of the moulded parts are higher than for the other process variants. As an example for the order of the size of the required tolerances, the flatness tolerance of a joining part with flat welding geometry and lateral dimensions in the range of 100mm x 100mm shall be mentioned here. For such an assembly, a flatness tolerance of maximum 0.08mm would be applied. Smaller deviations can be compensated for by higher clamping forces, but will lead to stresses within the assembly after the welding process.
QUASISIMULTANEOUS-MOVEMENT – Unlike a contour welding process, simultaneous and quasi-simultaneous welding involves a relative movement of the assemblies to each other. Usually, a so-called weld rib is provided on the laser-absorbing half of the part, which is melted off during processing. The laser-transparent part moves towards the laser-absorbing part. When the laser is switched off at the end of the process, a cooling phase follows in which the material shrinks as it cools down. In this context, it is important to consider the relative movement as well as the contraction during the cooling phase in the design. Usually the joining path for components with dimensions in the range of 100mm x 100mm is about 0.1-0.5mm.
QUASISIMULTANEOUS-MELT – In simultaneous and quasi-simultaneous welding, the melting of a joining path as described above displaces molten material from the joining zone. It is important to provide sufficient space for the displaced melt in the adjacent areas of the joining zone. Since this melt is usually aesthetically unattractive or – in the case of glass fiber-reinforced materials – poses a risk of injury during subsequent manual processing, it is additionally recommended to provide a cover.